The Cell and Gene Therapy Catapult’s (CGT Catapult) Braintree Manufacturing Innovation Centre (Braintree MIC) is designed to support cell and gene therapy developers to accelerate the development of their Good Manufacturing Practice (GMP) manufacturing operations for advanced therapies at a clinical and commercial scale.
Following a successful inspection by the Medicines and Healthcare products Regulatory Agency (MHRA), Braintree MIC received an MHRA Manufacturers and Importers Authorisation for Investigational Medicinal Products (MIA(IMP)) and associated GMP certificate.
This license allows therapy developers collaborating at the site in Braintree to develop their own advanced therapy manufacturing capabilities and contribute to the growing number of advanced therapy medicinal products (ATMPs) that are being developed, manufactured, and exported annually in the UK.
Significant transformations were required at Braintree MIC to establish the site as a centre for cutting-edge ATMP manufacturing development. The original site was repurposed to equip Braintree MIC with a robust infrastructure to support manufacturing, and several new game-changing capabilities were established.
This blog outlines how we transformed the site at Braintree to deliver an MHRA-licensed, state-of-the-art GMP facility for ATMP manufacturing development; leveraging specialist expertise and technologies to drive down manufacturing costs and help increase patient access to these life-changing treatments.
Establishing a skilled team
Advanced therapy manufacturing processes are complex, requiring specialised techniques and precise aseptic manipulation of biological materials. Skilled personnel are needed to deliver these processes to ensure adherence to strict quality standards and for their ability to drive optimisation.
At CGT Catapult’s Braintree MIC, 78 staff were retained and transferred across from the previous site owner, undergoing an in-depth skills analysis and role mapping process which led to the upskilling of the full cohort to work on advanced therapy GMP manufacturing processes.
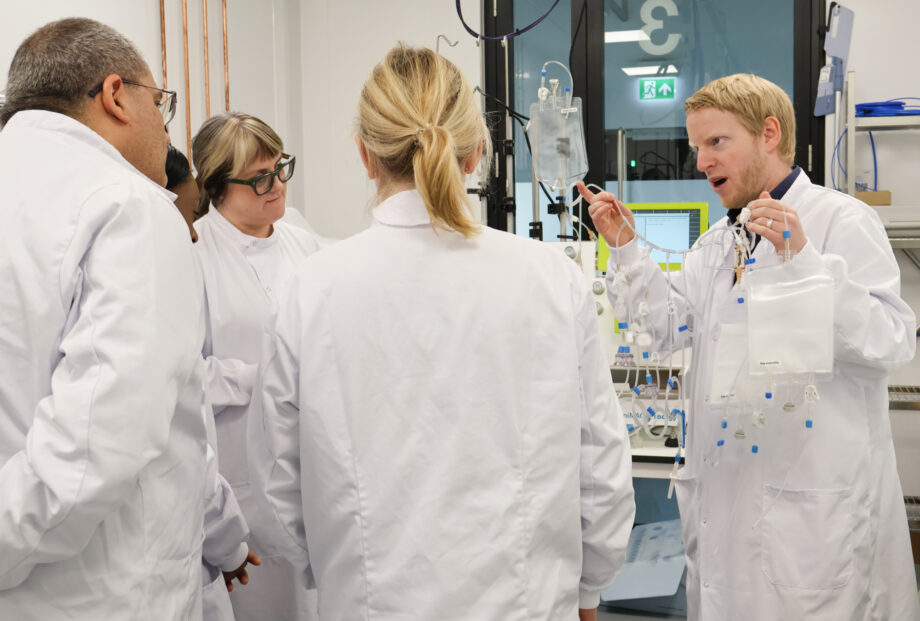
Alongside on-site training provided by CGT Catapult’s experts, upskilling was supported through the organisation’s Online Training Platform which hosts a diverse range of GMP-oriented training resources, including content on bioreactor systems, gowning for GMP environments and flow cytometry.
The site also serves as a training ground for industrial placements and apprenticeships through the Advanced Therapy Apprenticeship Community (ATAC). The ATAC programme, coordinated by CGT Catapult, provides work experience within the advanced therapies sector and helped facilitate the recruitment of skilled employees to support the expansion of the MIC’s capabilities.
Both the Online Training Platform and the ATAC programme are available to collaborators looking to establish or upskill their own manufacturing and technology teams.
Manufacturing according to GMP
GMP compliance is essential when manufacturing all human medicines, including advanced therapies, as it ensures companies manufacture their products to a high and consistent quality that is safe for patient use. An essential tool to support this is a Pharmaceutical Quality System (PQS) which is vital for maintaining a standardised and accessible archive of critical processes.
A robust PQS ensures the site is positioned to demonstrate compliance to regulators, and the team at Braintree MIC have developed a new suite of operational and quality processes that have been embedded within the PQS.
Controlled training documents and Standard Operating Procedures (SOPs) within the PQS also ensure that technicians are well-trained and operations at the site are performed at the highest technical and compliance standards.
This quality driven framework of operation typically takes up to two years to build and validate, and both CGT Catapult’s Braintree and Stevenage MIC’s allow collaborators to utilise an established PQS for human medicinal products for their own ATMP manufacturing needs.
Learn more about our industry-leading Manufacturing Innovation Centres
A robust data integrity programme
Another essential asset that ensures high quality and GMP compliance standards are maintained at Braintree MIC has been a comprehensive data integrity programme.
Reliability and accuracy of data is intrinsic to enabling the manufacture of consistently high-quality therapeutic products. The programme developed at Braintree MIC incorporates current regulatory and industry best practice guidance, using a holistic method to effectively govern data integrity.
The programme includes guidance and instructions on topics including proactive assessment of data vulnerabilities throughout the data lifecycle, risk focused control mechanisms, and the importance of establishing a strong quality culture within all levels of the organisation.
This approach is essential for all aspects of ATMP design, innovation, and manufacture, and our collaborators can leverage the robust processes we have put in place to streamline their ATMP development journey.
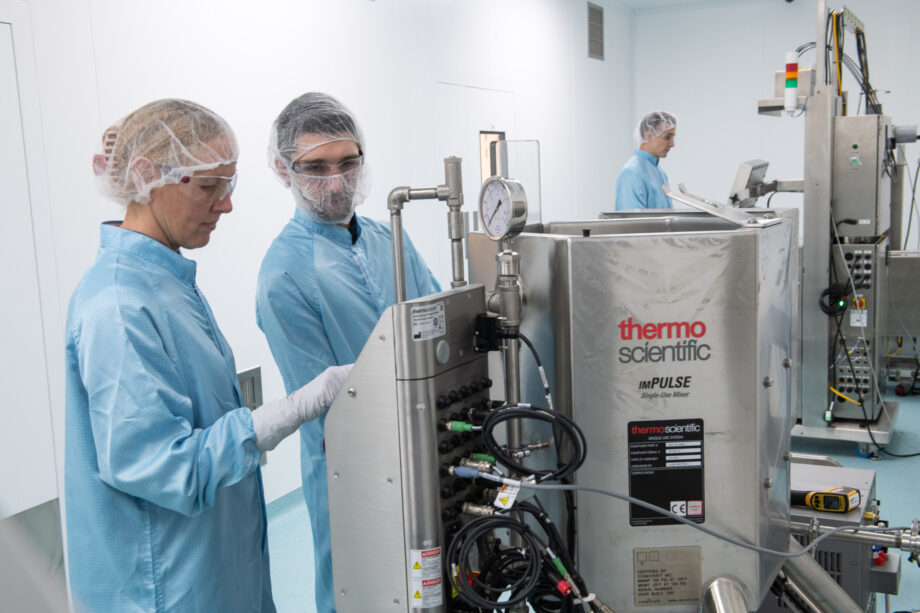
The manufacturing capability demonstration
Once the facility has been set up and the manufacturing process established, it is essential to carry out repeated demonstrations of capability. Completing demonstration or “engineering” runs can help to assess process consistency, and successful runs provide evidence to regulatory bodies that the process and surrounding infrastructure can consistently meet product specifications.
Part of the capability demonstration at Braintree MIC involved the transfer and upscaling of the CGT Catapult’s adeno-associated virus (AAV) vector production platform, developed at its laboratories in Guy’s Hospital, London, from two to 50 litres in a GMP environment.
Scaling up AAV manufacturing processes is complex and involves a high level of expertise and specialised equipment. New technologies at Braintree MIC such as Thermo Scientific DynaDrive Single-Use Bioreactors, helped to facilitate the upscaling process; fundamental to the upstream phase of AAV production, their highly configurable design reduces the significant footprint and costs typically associated with upscaling manufacturing.
The analytics associated with the platform were also transferred into the GMP cleanroom module following pre-qualification at the site’s Manufacturing Sciences and Technology (MS&T) and Analytical Development (AD) laboratories, and process development was carried out to ensure the 50 litre process was reproducible and suitable for technology transfer to other GMP sites.
This project resulted in the successful production of several robust 50 litre batches in GMP conditions, thanks to the scaling solutions and optimisation strategies introduced by the team. The CGT Catapult have been able to use the expertise gained through this process to support new therapy developers to establish, optimise and scale-up their own AAV manufacturing processes.
The scalable AAV manufacturing process developed at Braintree MIC has also been proven as successfully transferable through the LifeArc, MRC and BSGCT Innovation Hubs for Gene Therapies, demonstrating the site’s contribution towards increasing academic and industry access to GMP manufacturing for gene therapies and supporting the UK’s strength in the sector.
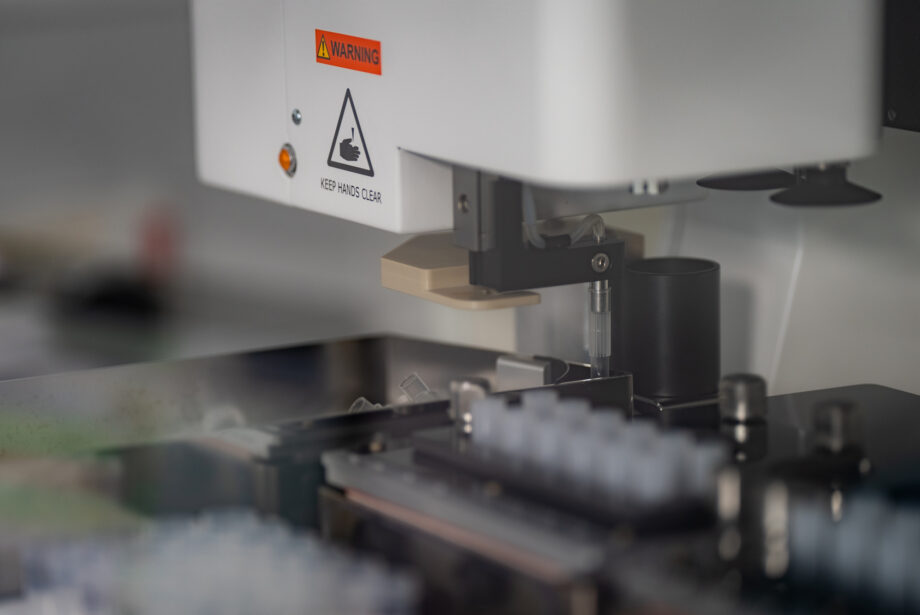
Digital and automation
Throughout the development and manufacture of advanced therapies, Process Analytical Technologies (PAT) can help to maximise process control and product quality, increase throughput and reduce costs.
Innovative new technologies were introduced into the GMP cleanroom module at Braintree MIC to establish this game-changing capability, including Raman spectroscopy, which contributes to a greater understanding of the manufacturing environment through real-time process monitoring and analysis. Real time collection of digital data that describes a manufacturing process is essential to maintain a high standard of data integrity, control and reduces risk to patient safety.
In collaboration with Autolomous, we have also digitised the on-site AAV manufacturing process, integrating critical manufacturing systems into a digital platform to enable real time control and data acquisition, as well as digitising essential Batch Manufacturing Records (BMR).
These state-of-the-art tools represent just a few of the transformational capabilities at Braintree MIC that can help advanced therapy developers make the transition to digitised processes.
Securing the license and beyond
An inspection was carried out by the MHRA at Braintree MIC at the end of 2023, and the site was later issued an MIA (IMP) license in February 2024. This success demonstrates the significant effort involved in transforming the infrastructure, technology, and workforce to establish Braintree MIC as a state-of-the-art centre for ATMP manufacturing development in the UK.
CGT Catapult are exceptionally proud of Braintree MIC’s transformation and the team who supported this journey. Looking forward, the team seek clinical and commercial collaborators looking for support to overcome their advanced therapy development challenges and establish their own robust GMP-compliant manufacturing processes.